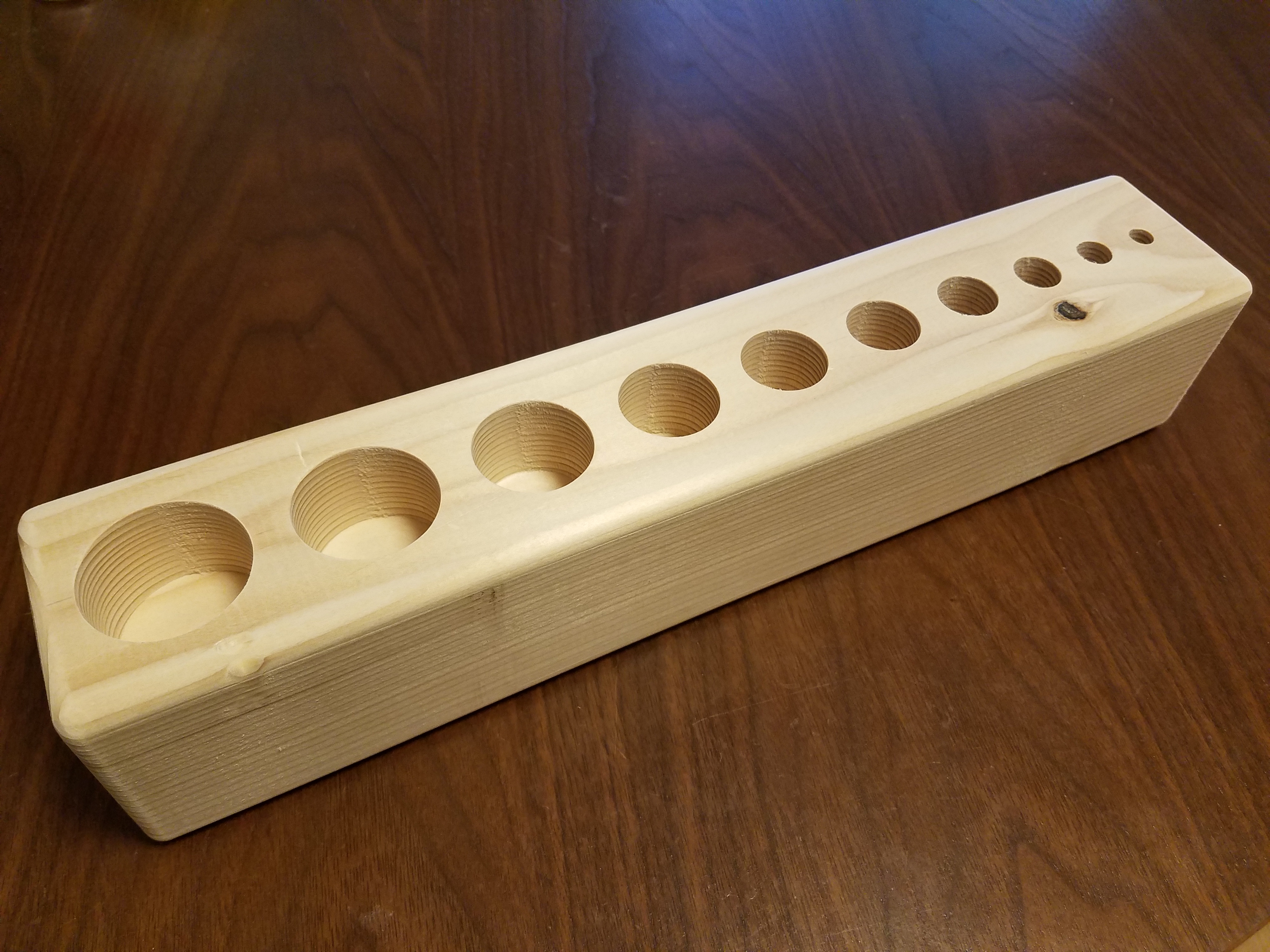
ファブラボでの工作で、前回円柱部分を作成できたので今回は土台部分を作っていきます。
関連記事:ファブラボで3Dプリントしてきたよ。
土台の形状
おさらいとなりますが、土台の形状は以下になります。
この形状から、長い柱のような木材をCNC切削機で削っていく方法をとることになりました。
CNC切削機
フィラメントを溶解して一層ずつ積み上げていくのをプラスの3Dプリンターとするのであれば、CNC切削機はマイナスの3Dプリンターです。
木材や金属など、あらかじめ決まっている大きさのものからコンピューターで送られたデータに従って物体を削って切り出す機械です。
積層型の3Dプリンターと違って、もともと一つの物体から削り出されるので素材の特性も保たれるのが特徴です。
CNC切削機は材料加工部分にドリルが設置されていて、コンピューターからこのドリルの動き(ツールパスといいます)が送られて材料を加工していきます。
ドリルの動く軸は、縦横高さ(XYZ)の3軸加工と、それに2つの回転軸(XYZBC)を加えた5軸加工がありますが、今回は一方向から穴を掘るだけなので。3軸加工を使います。
曰く、『5軸加工は複雑すぎて失敗しやすいので、なるべくやらない方がいい!』とのこと。
今回は、手間も考慮して以下のように作っていくこととしました。
- ドリルの長さが足りないので、円柱を入れる穴の深さを5cmから3cmに変更(前回記事の通り)
- 一番小さな穴は、細すぎてCNC加工機で削れないのでアナログのドリルで開ける
- エッジのトリム(角丸)はアナログのビットでかける
- 側面のアーチ状の窪みは削るのが手間なので、廃止(機能的な意味はほぼないので)
下準備
まずは木材を調達します。
近所の東急ハンズで柱状の木材を買ってきました。
70mm×70mm×1000mmで、1,800円くらい。
設計したモデルの太さとぴったり一致するものが見つからなかったので、モデル側のサイズを変更します。
太さが70mm×70mmになるように、モデルを修正しました。
次に、長さを土台の長さと同じになるように木材をカットします。
電動の丸ノコが付いたスライド型切断機で切断します。これもアナログです。
これで切削の準備が整いました。
ツールパスの作成
くり抜く穴部分のツールパスをFUSION360で作成します。
ツールパスの作成は「CAM」作業スペースを使います。
しかしながら、この設定はかなり複雑なのでほぼファブラボの方にやってもらう形になりました。
ざっくり説明すると、以下のような工程からなります。
- 使用するツール(ドリル)の登録・設定
- 切削対象の材料(木材)の設定
- 削り方(ミーリング・3軸・座標系)の設定
- 使用する材料サイズの入力
- 切削対象箇所(ポケット)の指定
- ピッチ(軌跡の間隔)の設定
- 切削層数(複数深さ)の設定
- 仕上げ代の設定
- ツールパスの出力
- シミュレーション
各設定項目ともに、実際の材料の硬さやドリルの強度、アナログ加工とデジタル加工の役割分担などに関する理解が必要になりますので、経験者から伝授してもらわないと厳しいですね。
ここまで完了したら、CNC切削機にPCをつないでデータを送信していきます。
切削開始
まずは準備した木材を機械にセットします。
コンピューターで設定した通りの結果を得るためには、座標軸が実態と完全に一致していなければならないので、ちゃんと台と平行に設置できているか、微調整しながら設置します。
設置できたら削っていきます。
すごい大きな音がします……ここからだいたい1時間ほどかかります。
全ての穴を掘り終わって完了。これで土台の上部分が完成しました。
ちゃんと設定した通りにできてますね。
アナログ加工で仕上げ
最終工程として、各種アナログ加工で仕上げていきます。
まずは、一番細い穴ができていないので、ドリルで削ります。
これは単純でドリルで縦穴を開けるだけです。
次に、トリマービットで角丸をつけていきます。
トリマービットというのは以下のような感じのドリルのことで、これを材料のカドにあてて削ることで角丸がつきます。
ベアリングのコロが付いているものが使いやすくてオススメですね。
こちらで削って以下のように、角丸がつきました。
あとは削り部分のささくれている所や表面を紙やすりで磨いて、きれいにして完成です。
まとめ
結構単純な形状だと思っていたのですが、木材を削っていくところはかなり工程も多く、作業は複雑でした。
あとは何と言ってもやはりアナログ加工の活躍する場面が多い!ということですね。
デジタル加工が取りざたされている現在ですが、全ての工程をデジタルにするのではなくて、アナログとデジタルの得意分野を見極めて使い分けていくことが、制作の幅を広げるポイントとなるでしょう。